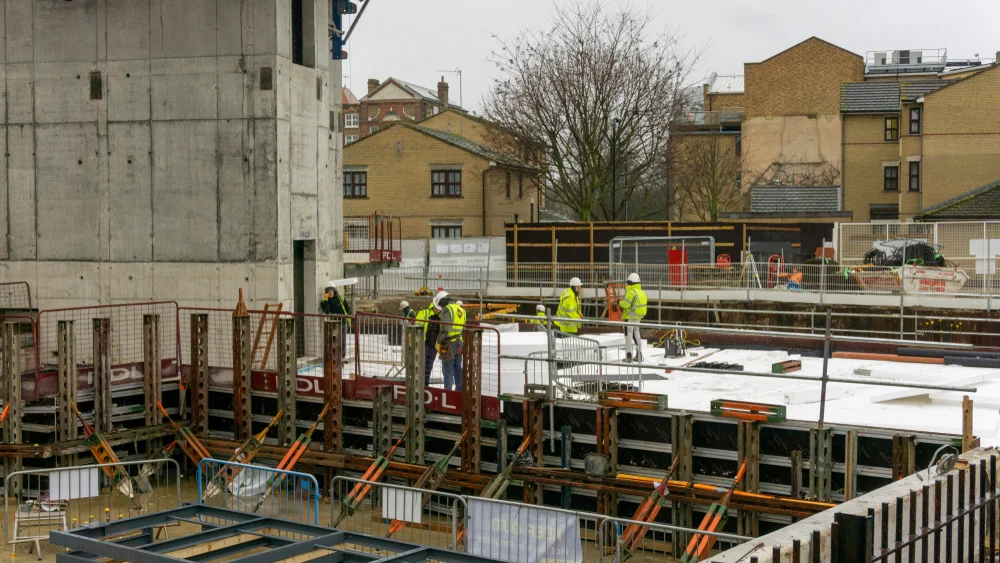
The Hidden Dangers of RAAC Planks and Their Safety Risks.
The Hidden Dangers of RAAC
RAAC planks pose safety risks as their open structure risks compromised bonding and water penetration.
Although widely used from the 1950s-1990s, the UK discontinued RAAC due to these hazards. However, many buildings still contain risky RAAC elements, needing urgent inspections and redesigns.
For 10 years, Structural Repairs has offered invaluable expertise in addressing this pressing issue.
Specifically, they thoroughly evaluate existing RAAC structures and provide risk mitigation solutions.
With extensive RAAC assessment experience, Structural Repairs has the knowledge and capabilities to tackle this critical building safety problem.
The Hidden Dangers of RAAC Planks
Many institutions and homes contain risky RAAC planks.
These Reinforced Autoclaved Aerated Concrete planks have inherent hazards compromising building integrity.
Specifically, RAAC’s open structure risks inconsistent steel bonding and water penetration, weakening planks over time.
This increases collapse and failure risks. Additionally, RAAC planks often have short steel reinforcement, further compromising stability.
Therefore, building owners and authorities must thoroughly inspect, identify RAAC buildings, and take necessary safety measures for occupants.
The Importance of Urgent Inspections
Experts must urgently inspect RAAC plank buildings. Specifically, these inspections assess integrity and mitigate risks. Additionally, proactive checks play a crucial role, identifying potential RAAC hazards.
In particular, RAAC’s open structure can lead to poor steel bonding and water penetration, compromising stability over time. Through thorough inspections, experts can detect deterioration signs like corrosion or cracking that compromise integrity.
Inspections also determine the required remedial action extent to ensure occupant safety. By promptly identifying and addressing issues, accidents and potential harm can be prevented.
Therefore, urgent inspections are critical to protect occupants and preserve building integrity.
Understanding the Safety Risks
To address RAAC plank risks, understanding potential hazards is crucial.
RAAC planks have inconsistent steel bonding, compromising integrity. This leads to higher collapse and failure risks, especially under heavy loads.
Additionally, RAAC’s open structure risks water penetration, causing moisture accumulation that weakens planks over time.
Inspections and remedial designs must account for these hazards. The priority is ensuring the safety of RAAC buildings.
Remedial Design for RAAC Planks
Experts must implement proper RAAC plank remedial design to address risks.
Specifically, remedial measures involve developing solutions that mitigate RAAC hazards like poor bonding and water penetration.
Additionally, designs should improve structural integrity, durability, and ensure safety standard compliance.
Implementing safety protocols is crucial to ensure proper adherence. Thorough inspections, industry guidelines, and RAAC experts are required to properly assess RAAC planks.
In particular, assessing involves conducting thorough inspections evaluating structural integrity, steel bonding, and water penetration issues. For instance, inspection methods include hammer tapping, cover meter scanning, and petrographic analysis.
The goal is identifying deterioration signs and determining remedial actions
- Visual Inspection: A visual examination is conducted to identify any visible signs of damage, deterioration, or corrosion on the surface of the RAAC elements.
- Non-Destructive Testing: Techniques such as ultrasonic testing or ground-penetrating radar can be employed to assess the internal condition of the RAAC elements without causing any damage.
- Moisture Testing: Moisture meters or moisture probes can be used to measure the moisture content within the RAAC elements, which can indicate potential water penetration issues.
- Load Testing: Load tests can be performed to evaluate the structural capacity of the RAAC elements and determine if they can safely support the intended loads.
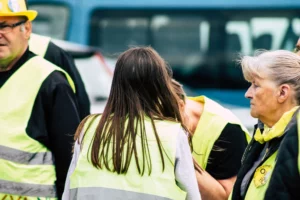
Developing a Management Plan
Developing an RAAC plank safety risk management plan requires a systematic approach. First, qualified professionals must thoroughly assess RAAC element conditions. This identifies potential hazards.
Professionals like structural engineers should have RAAC experience. Once risks are identified, develop a maintenance strategy. This addresses the risks.
The strategy should include regular inspections. It should monitor RAAC planks. This ensures prompt deterioration and damage identification and remedy.
Additionally, implement risk mitigation measures. These minimize accident and failure chances. Measures may involve plank reinforcement.
They may involve sealing cracks and voids.
They may even involve RAAC element replacement with reliable materials.The management plan should also include
- Clear guidelines for communication
- Coordination between relevant stakeholders
- Necessary actions are taken in a timely manner by building owners, maintenance personnel, and engineering consultants
The Role of Structural Repairs in RAAC Planks Safety
Structural Repairs plays a crucial role ensuring RAAC structure safety through expertise and specialized services.
Specifically, with in-depth RAAC knowledge and extensive experience investigating and assessing these structures, Structural Repairs offers valuable client support.
Here is how Structural Repairs contributes to RAAC safety:
- Identification of RAAC use: Structural Repairs can accurately identify the presence of RAAC elements in buildings, helping clients understand the potential risks associated with these structures.
- Assessment of condition: Through thorough inspections and assessments, Structural Repairs evaluates the condition of RAAC elements, identifying any weaknesses or deterioration that may compromise their safety.
- Design of additional support structures: Structural Repairs provides design services for the installation of additional support structures, ensuring the stability and integrity of RAAC elements.
- Replacement and remediation: In cases where RAAC planks pose a high risk, Structural Repairs can design solutions for their replacement or remediation, offering safer alternatives.
Structural Repairs plays a crucial role in safeguarding the integrity and safety of RAAC structures. Using the very latest technology to help create detailed reports.
Designing Solutions for High-Risk Planks
Developing and implementing reinforcement strategies for high-risk RAAC planks is essential to ensure building safety.
Specifically, designing retrofit solutions and risk mitigation strategies is crucial to address RAAC safety concerns.
Carefully planned and executed, these solutions must target specific issues identified in each building. For instance, retrofits may include adding reinforcement, improving bonding, or applying protective coatings to prevent water penetration.
Additionally, risk mitigation could involve regular inspections, maintenance, and monitoring to detect deterioration signs.
Importantly, building owners, engineers, and professionals should collaborate to develop and implement these solutions, ensuring long-term safety of structures with risky RAAC planks.
Ensuring the Safety of Buildings With RAAC Elements
To ensure the safety of buildings with RAAC elements, regular inspections and remedial design measures must be implemented.
Here are four reasons why these actions are crucial:
- Importance of regular maintenance: Conducting regular inspections enables the early detection of any issues or deterioration in RAAC elements. Through this proactive approach, timely repairs or replacements can be performed, thereby preventing potential safety hazards.
- Impact of weather conditions on RAAC elements: RAAC elements are susceptible to various weather effects, including moisture, freeze-thaw cycles, and UV radiation. By performing regular inspections, any damage caused by these factors can be identified, prompting the necessary remedial design measures to be taken.
- Ensuring structural integrity: Conducting regular inspections identifies any structural deficiencies in RAAC elements promptly. Subsequently, remedial design measures such as additional support structures can be implemented in a timely manner to ensure the overall stability and safety of the building.
- Compliance with safety regulations: Regular inspections and implementing remedial design measures align with safety regulations and building codes. By adhering to these standards, building owners can ensure the well-being of occupants and mitigate potential liabilities.
What have we learnt?
RAAC plank safety risks require urgent inspections and remedial design.
Specifically, RAAC’s open structure can compromise building integrity, posing a serious threat.
With their expertise, Structural Repairs will play a crucial role addressing this issue. Contact us today.
It is essential to ensure RAAC building safety by implementing management plans and additionally designing solutions for high-risk planks.