Enquête sur les essais non destructifs pour une entreprise de services publics
Structural Repairs a été confronté à une tâche complexe en réalisant un contrôle non destructif (CND) pour l'usine de traitement des eaux d'une société de services publics. Les principaux défis consistaient à inspecter des espaces confinés avec un accès limité tout en assurant la sécurité des travailleurs et en évitant des arrêts coûteux de l'usine. Le faible éclairage, les perturbations potentielles de la communication et la nécessité d'identifier des défauts infimes dans des zones difficiles d'accès ont encore compliqué la tâche.
Le projet nécessitait une solution innovante capable de surmonter ces obstacles tout en fournissant des évaluations précises et détaillées des infrastructures critiques. Les méthodes d'inspection traditionnelles n'ont pas permis de répondre à ces exigences multiples, ce qui a nécessité une nouvelle approche alliant sécurité, efficacité et précision dans les inspections d'espaces confinés.
Structural Repairs deployed a versatile indoor drone with advanced industrial inspection capabilities, featuring cutting-edge technology specifically designed for confined space inspections. This innovative solution leveraged state-of-the-art LiDAR-based mapping, advanced collision resilience, and high-precision imaging capabilities to conduct a comprehensive NDT survey without compromising safety or operations.
The drone's robust, collision-tolerant design enabled close-up inspections in tight areas, while its advanced imaging system combined high-definition visual cameras with thermal sensors to detect minute defects. The powerful, dust-proof lighting system and versatile modular payload system ensured thorough inspections even in challenging conditions.
This solution offered a safe, efficient, and cost-effective alternative to traditional inspection methods, eliminating the need for plant shutdowns and significantly reducing safety risks associated with confined space entry.
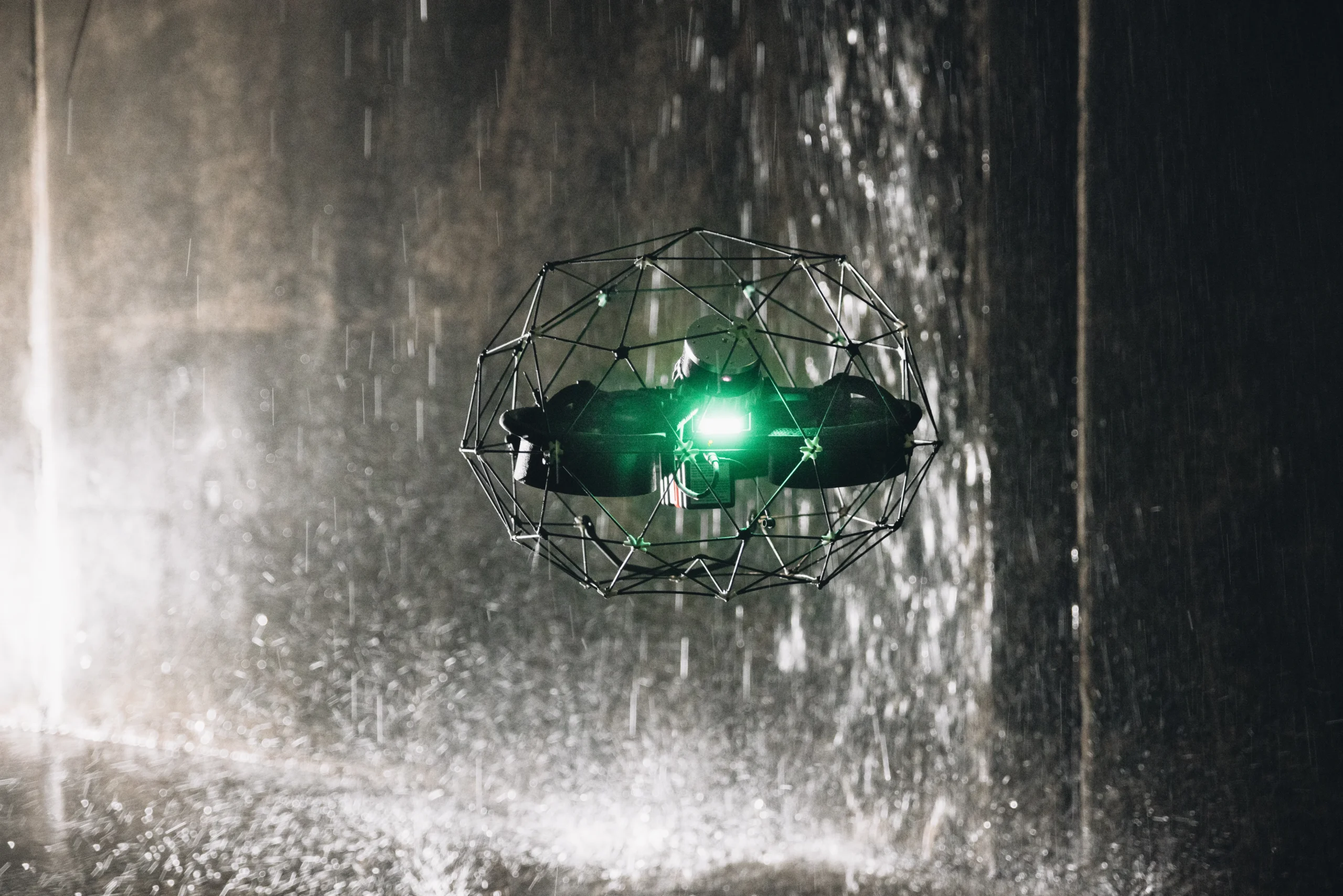
Skilled operators navigated the drone through the water treatment plant's complex confined spaces, including narrow pipes, tanks, and intricate structural components. The drone's collision-resistant design allowed it to bounce off surfaces and continue unimpeded, accessing areas impossible for human inspectors.
As it moved, the drone's high-definition cameras and thermal imaging sensors captured detailed visual and thermal data, identifying a wide range of potential defects from surface corrosion to hidden leaks. The 3D live mapping feature, powered by LiDAR, enabled real-time visualization and assessment of the inspected areas.
The FlyAware engine provided centimeter-level accuracy, ensuring precise location and mapping of even the smallest defects. Throughout the inspection, the drone's powerful dust-proof lighting system ensured clear visibility in dark areas, while the Return-To-Signal feature maintained connectivity in weak signal zones.
This technology-driven process allowed for a thorough inspection of the entire facility, providing unprecedented access to hard-to-reach areas and gathering detailed data without disrupting plant operations.
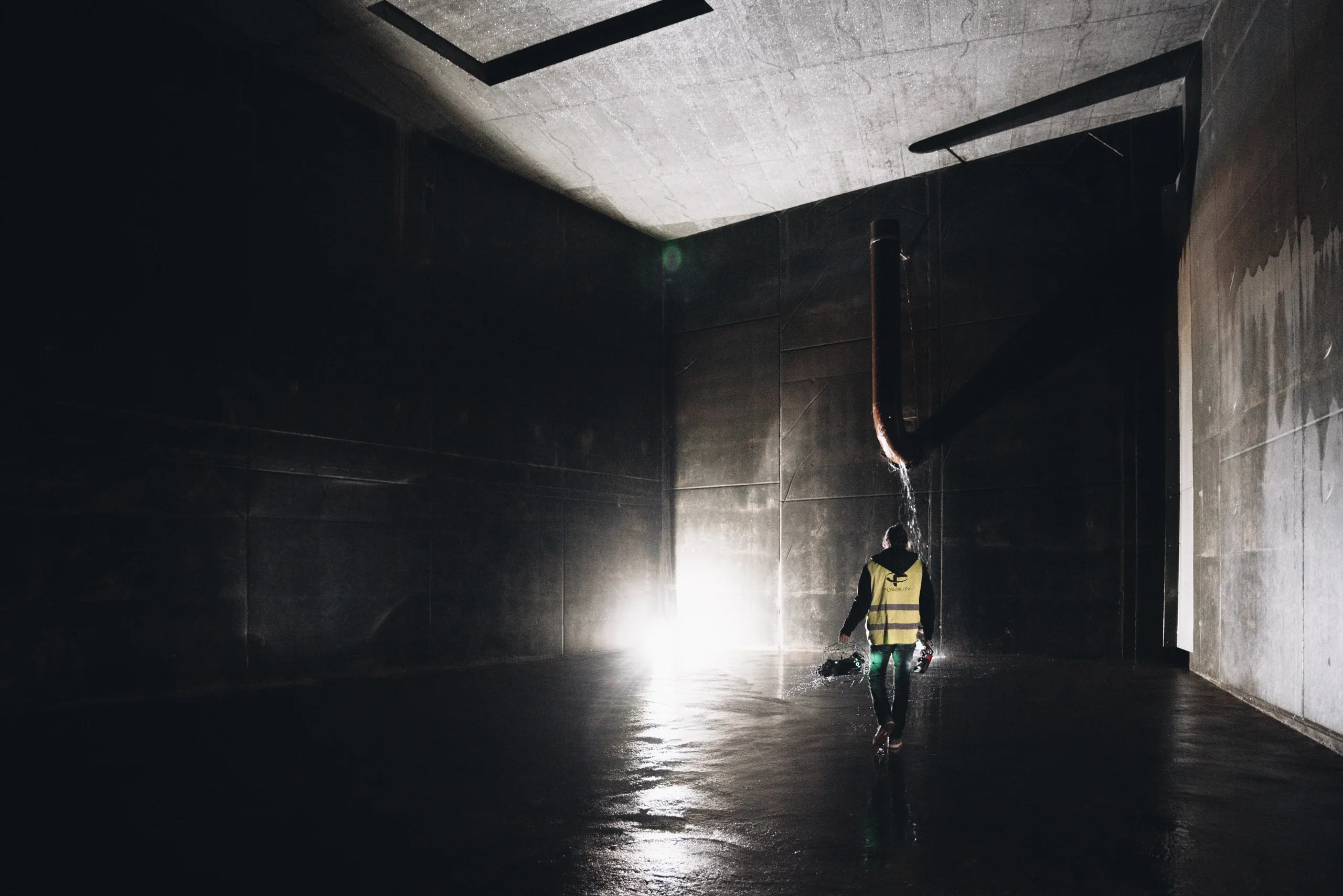
L'approche innovante de l'étude CND a apporté des avantages significatifs à l'entreprise de services publics. La sécurité sur le lieu de travail s'est nettement améliorée, car le personnel n'a plus eu besoin de pénétrer dans des espaces confinés dangereux. Simultanément, la nature non intrusive de l'inspection par drone a permis une exploitation ininterrompue de l'usine, ce qui s'est traduit par des économies substantielles. Les données de haute précision recueillies ont permis la création d'un jumeau numérique complet des espaces confinés de l'installation, ce qui constitue un atout inestimable pour la planification future de la maintenance et l'optimisation opérationnelle.
La cartographie détaillée des défauts produite par l'étude a permis de développer des stratégies de réparation prioritaires et ciblées. Cette approche pourrait prolonger considérablement la durée de vie des infrastructures essentielles. En outre, le succès de cette méthode d'inspection révolutionnaire a établi une nouvelle norme industrielle pour l'évaluation des espaces confinés dans les installations de services publics, démontrant le potentiel de la technologie avancée pour révolutionner les processus d'inspection traditionnels.
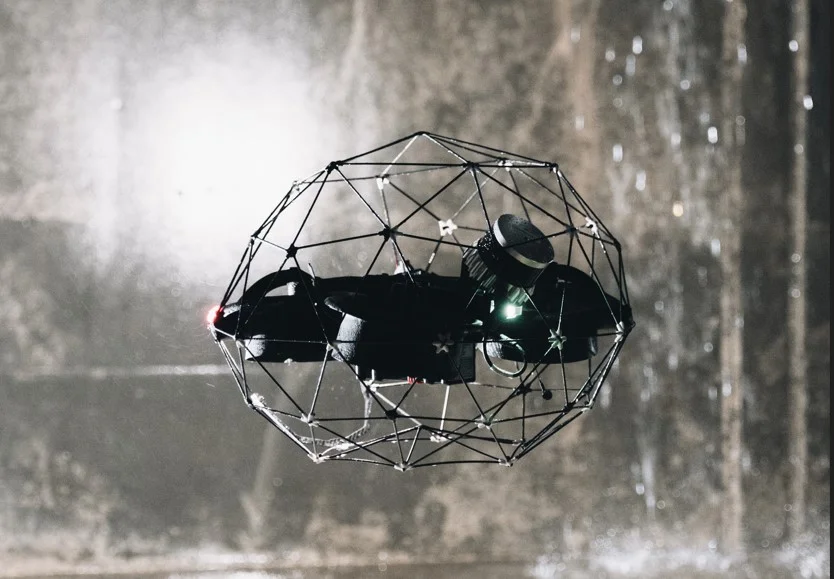
Structural Repairs est un spécialiste mondial de premier plan